Automated Material Handling
Maximize Space.
Improve Efficiency.
Achieve 99.9% Accuracy.
Automated Material Handling (AMH) designs and installs low-risk automated storage solutions for optimized space, picking and replenishment, serving businesses in Kentucky, Tennessee, and southern Indiana.
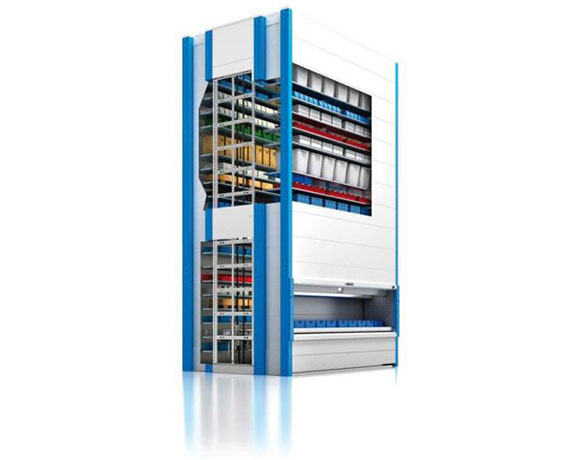
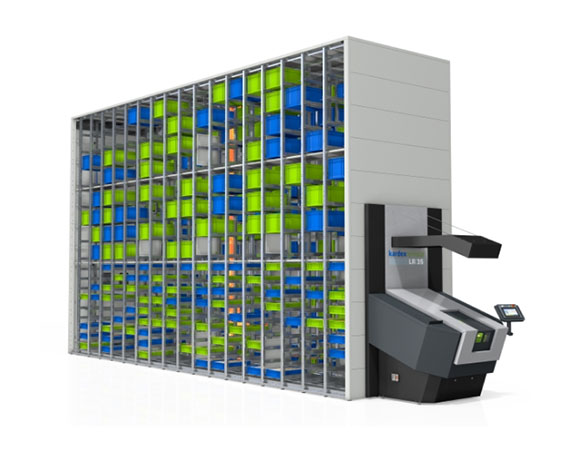
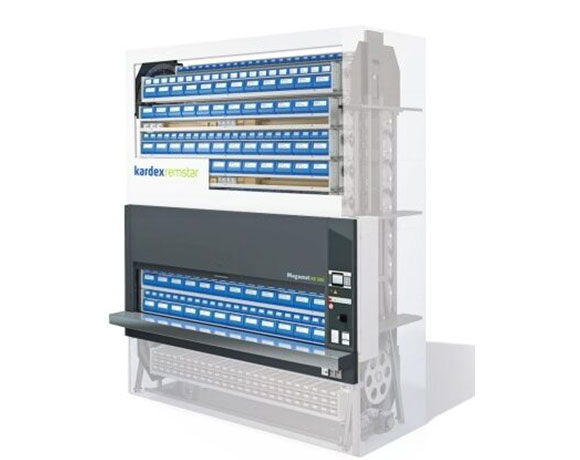
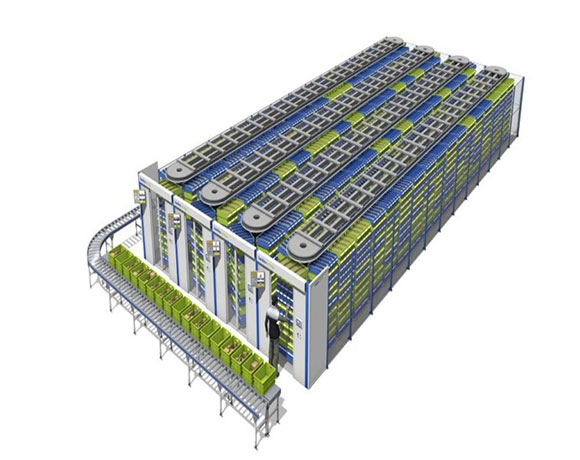
GET A FREE FACILITY EFFICIENCY EVALUATION WITH AN AMH ENGINEER
WHY AUTOMATE?
make the most of your space
- Get up to 85% of your floor space back. Less clutter, more productivity
optimize your operations
- Reduce labor costs, invest in other areas, and increase long-term profits.
speed up your workflow
- Meet demand 3x faster with high-speed picking. Accelerate every order with confidence.
Achieve peak Accuracy
- Reach 99% accuracy to reduce costly errors. Protect your brand, and keep your customers satisfied.
Prioritize Safety
- Protect your team from unecessary strain or injury. Smarter systems = safer people.
For the full breakdown, visit our resources page.
The AMH Approach to Material Handling Solutions
Every AMH partnership is custom.
Because you have a unique facility with unique goals and constraints, AMH always starts with an on-site visit to develop a custom material handling solution.
Every AMH partnership is a seamless transition
We assist with every step of the automating transition process by offering onsite inventory relocation, organization, and slotting services.
Every AMH partnership is worry-free.
We back all material handling solutions with onsite service and support to keep you running at peak efficiency at all times.
The Automated Material Handling Process
01
Consultation
Start with a quick, no-obligation call to discuss your material handling challenges, goals, and current operations. We’ll determine if automation can move the needle for your facility.
02
Solution Design & Proposal
Our experts analyze your needs and develop a tailored system architecture. You’ll receive a clear proposal with recommended solutions, budget expectations, and projected outcomes
03
Installation & Support
From integration to installation, we handle the details—coordinating logistics, vendor partners, and timelines. After launch, we stay involved to ensure system success and provide ongoing support.
share your facility goals with an AMH material handling systems expert to discover your next best automation step.
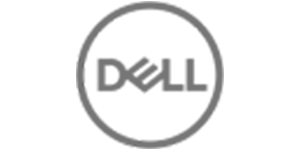
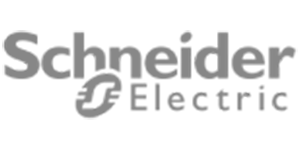
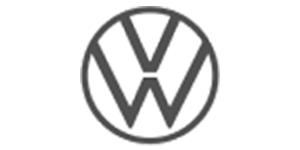
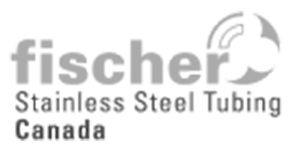
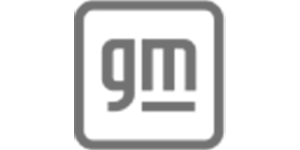
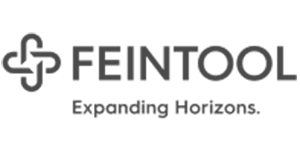
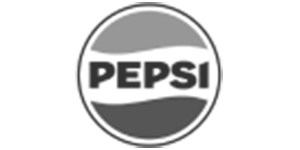

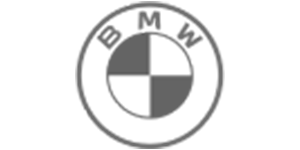
Customer Reviews
“
“
One was that they had the ability to provide all three types of equipment that we wanted, and two, the fact that they invited us to go visit three other factories with them, and were very open and candid about letting us talk to them. They went out of their way to make sure that we were comfortable with the equipment that we were buying. That tells you a lot when they let you walk in and talk to their other customers.
“
“
We shoot for 30% ROI and I don’t see why we won’t be able to pull that off. Our customer service level has increased considerably, especially since we got the Kardex, because we can pick, package and ship much faster than we could before. So, our overall customer satisfaction is up, too.
“
“
Make sure you take into account the shop floor inventory transactions that are going to have to take place—just the sheer volume of forklift moves to get a spot cleared out and the next piece of equipment up, and then back into that piece of equipment and up.
“
“
Don’t let the price scare you. It’s a lot cheaper to fill up your cubic feet than it is to purchase new square footage. It’s still cheaper than buying a building or making a building
“
“
We were looking, at the time, at upwards of 116 part numbers that we needed to manage, and a floor
space of about 7,300 square feet. And main body wire harnesses are very, very large, and very, very heavy components that take up a lot of space. So, that number of parts wasn’t going to fit in that small floor space.
“
“
…over the course of two weeks, we got all the components assembled and got the VLMs built. We had four towers. And then the next week after that, Kardex sent a representative who helped us program the system, get all the parts loaded into it, and train up the operators and some of the engineers and salaried employees in the plant as well, so we can help with any sort of downtime issues.
“
“
The AMH team was easy to work with, very attentive. Like any other company, ours has its own little intricacies you need to learn to be successful—but they were more than willing to take on those lessons. Definitely highly rated among the other vendors that I’ve worked with. They were easy to work with on things like changing the POs and doing amendments to the purchase orders.
Book a Free Consultation
Talk to our product experts about your facility’s needs, bottlenecks, and process goals.
We’ll share your custom automation opportunities, and calculate your short and long-term ROI.