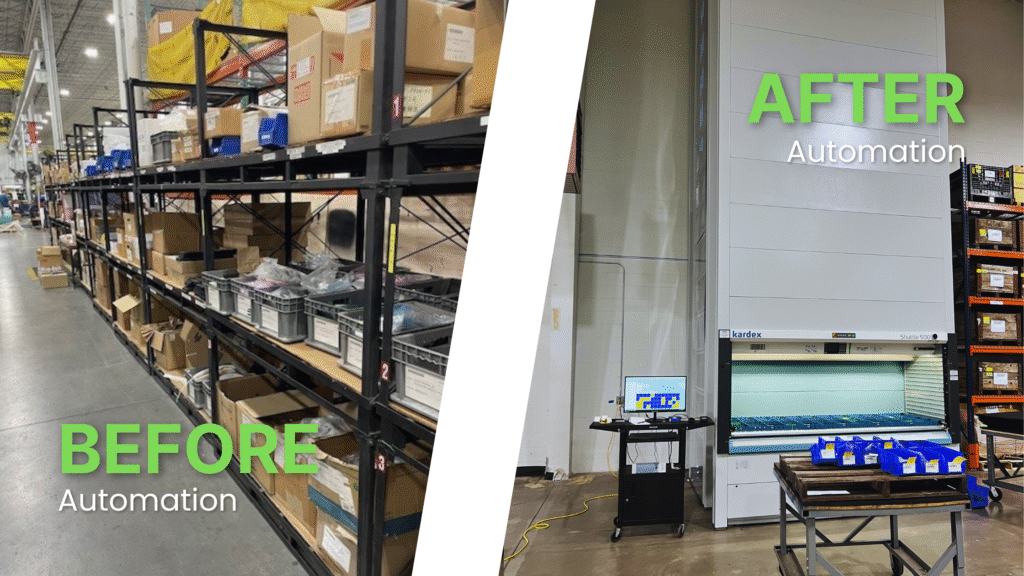
When inventory is hard to find, tools are misplaced, or SKUs are scattered across departments, productivity slows to a crawl. For manufacturers and distributors trying to meet tighter deadlines and higher demand with leaner teams, those delays don’t just hurt—they compound.
That’s why forward-thinking operations are embracing automated storage and retrieval systems (ASRS) to meet their facility’s exact needs. These systems don’t just save space. They create speed, structure, and clarity—turning disorganized floors into high-performance environments.
The Real Cost of Manual Storage
Traditional storage setups—think static shelving, pallet racks, and outdated bin systems—aren’t built for today’s pace. They take up precious floor space, rely on tribal knowledge, and often result in:
- Excess walking and wasted motion
- Slow pick times and mispicks
- Inventory discrepancies and stockouts
- Ergonomic risks from climbing and reaching
- Difficulty training new employees
A study by McKinsey showed that up to 60% of warehouse labor time is spent walking or searching for parts—a hidden cost that drags down throughput and frustrates teams.
Why Manufacturers and Distributors Struggle to Automate
Despite the clear advantages, many facilities delay automation. Why?
- “It’s working fine.” Familiar processes feel safe, even if they’re inefficient.
- Sticker shock. Automation seems expensive—until you calculate ROI from labor reduction, inventory accuracy, and faster throughput.
- Too many choices. With dozens of automation vendors on the market, it’s hard to know where to start.
- Fear of disruption. Change brings unknowns. A poorly scoped system can create more problems than it solves.
That’s where AMH steps in.
Automation That’s Smarter—and More Personal
Kardex systems are fast, scalable, and built for precision. But when combined with AMH’s consultative approach, they become purpose-built solutions designed around your actual workflows.
We don’t just drop equipment into your building. We help you evaluate your:
- Inventory profiles and SKU velocity
- Pick frequencies and ergonomic needs
- Floor space and vertical clearance
- Order volume and system scalability
- Existing WMS/ERP integration
Then we build the right system—from Shuttle XP VLMs to Horizontal Carousels—and fine-tune the process to deliver real operational gains.
Real-World Results Across Industries
Aerospace & Defense
Shuttle XP VLMs secure serialized tools and track mission-critical components with full auditability and access control.
Electronics Manufacturing
Vertical Buffer Modules (LR35) manage thousands of ESD-sensitive parts with dust-safe access and real-time inventory visibility.
Medical Device Assembly
Megamat RS carousels optimize cleanroom storage with FIFO tracking and secure batch inventory for regulatory compliance.
Automotive Lines
Horizontal Carousels deliver JIT components fast, reducing downtime and improving throughput.
Warehouse & Distribution
Integrated Kardex Power Pick software and multi-system setups drive faster order fulfillment and smart replenishment—even during peak season.
What Makes Automation Projects Succeed?
The most successful facilities follow five key steps:
- Evaluate internal processes. Automation can’t fix a broken workflow. Start with SOPs, training, and baseline metrics.
- Identify the right fit. Not all SKUs benefit equally. Medium-volume, high-pick items are a good starting point.
- Loop in IT early. Integration is smoother when software requirements are clear from the start.
- Pilot before scaling. Small rollouts allow teams to adapt and fine-tune.
- Secure buy-in. Frontline workers and leadership must understand and support the change.
From Concept to Completion: A Clear Path to Smarter Warehousing
One of the biggest hurdles manufacturers and distributors face with automation isn’t the technology—it’s the uncertainty of the process. When does it start? How long will it take? Who’s responsible for what?
At AMH, we eliminate uncertainty with a clear, structured implementation path. Every automated material handling system we install follows a proven project timeline designed to reduce disruption and keep your team informed at every step.
Check out our installation roadmap below:
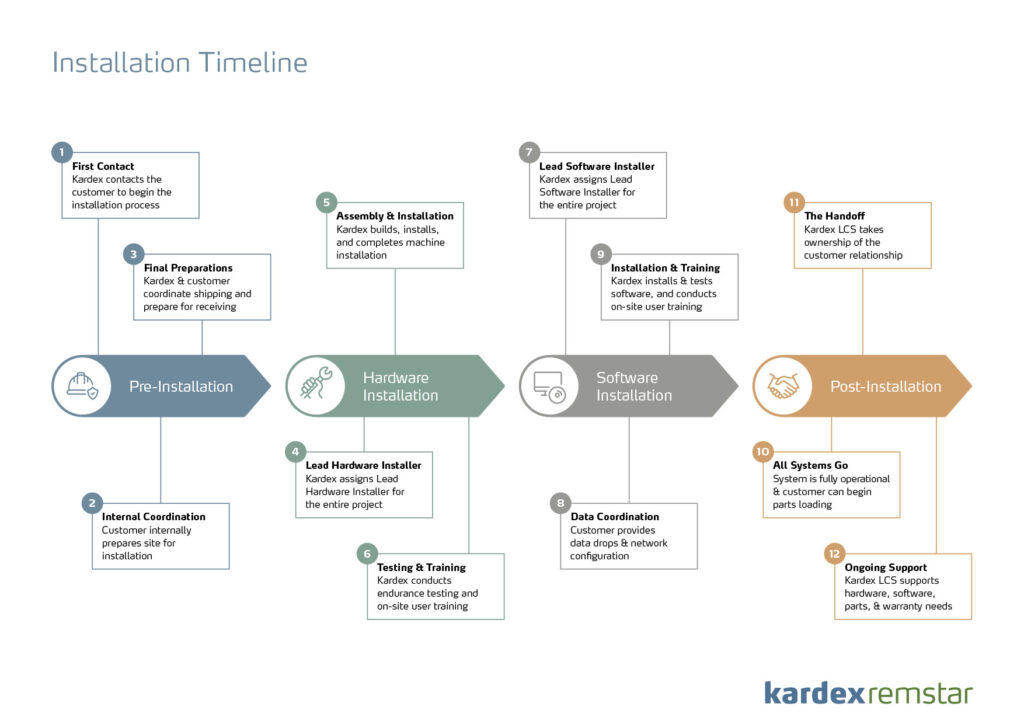
Your Competitive Edge Starts Now
Automation doesn’t have to be complex or overwhelming. With AMH and Kardex, it becomes a strategic lever for leaner operations, happier teams, and smarter growth.
As a certified Kardex distributor serving Tennessee, Kentucky, and Southern Indiana, AMH brings local expertise and tailored solutions to every project—from consultation to implementation.
Ready to turn your facility into a model of efficiency? Talk with one of our experts to discover your automation opportunities today.